Latest Nonwoven Fabric Equipment Technology: Driving Industry Innovation Trends
Release time:
2024-09-23
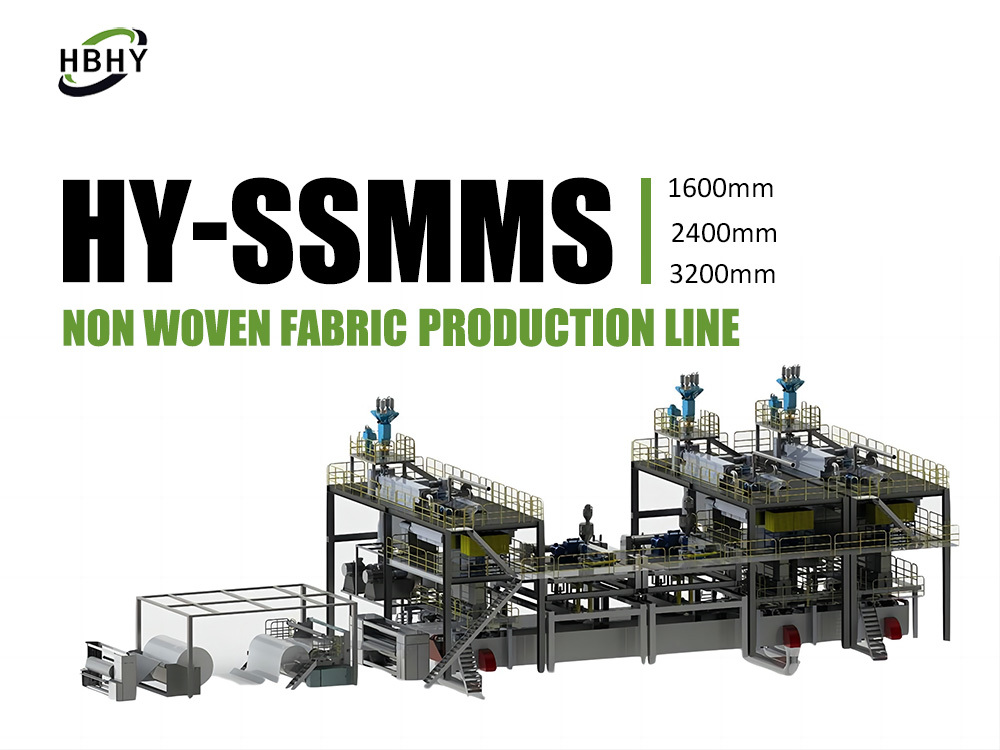
1. Introduction of Smart Production Lines
Smart manufacturing is becoming a new direction for the development of the nonwoven fabric industry. By introducing intelligent production lines and automated equipment, companies can achieve comprehensive monitoring and optimized management of the production process. The new generation of nonwoven fabric equipment integrates advanced sensors and control systems to monitor equipment operation, material consumption, and product quality in real time, significantly improving production efficiency and precision.
- Data-Driven Decision Making: With the combination of big data and IoT (Internet of Things) technology, equipment can collect and analyze data generated during production, providing scientific support for equipment maintenance, quality control, and production forecasting.
- Automated Operation: New intelligent equipment can automatically adjust production parameters, reducing manual intervention and minimizing errors and waste during the production process.
2. Environmental Protection and Energy-Saving Technology
As global environmental standards increase, nonwoven equipment is also moving towards energy-saving and emission-reducing development. The latest generation of equipment adopts more efficient energy management systems during production and minimizes waste emissions, helping companies achieve sustainable development goals.
- Low Energy Consumption Design: By optimizing the transmission system and controlling motor speed, the new equipment can effectively reduce energy consumption while ensuring output and quality.
- Waste Recycling System: Some equipment is already equipped with waste recycling devices, allowing for the secondary use of waste edges and materials produced during production, thereby reducing production costs.
3. Multi-Function Nonwoven Fabric Equipment
With the growing demand for multifunctional nonwoven fabric products, equipment manufacturers have launched integrated multifunctional equipment. This equipment can complete various processes on a single production line, such as spunbond, meltblown, and thermal bonding, meeting the production needs of different products.
- Modular Design: This design allows equipment to flexibly adjust and combine different process modules, enabling quick production switches between different types of nonwoven fabric products and improving the adaptability of the production line.
- Multi-Layer Composite Technology: The new equipment can produce multi-layer composite nonwoven fabrics, which have better physical properties and functional characteristics, widely used in medical protection, household cleaning, and other fields.
4. High-Efficiency Meltblown Technology
Meltblown nonwoven fabric, as an essential material for masks, protective clothing, and other protective products, is constantly advancing in production technology. The new meltblown equipment improves the uniformity and fineness of fibers by optimizing the structure of the spinneret and airflow control system, thereby enhancing the filtration performance and comfort of the nonwoven fabric.
- Nano-Level Fiber Manufacturing: By improving the meltblown process, it is possible to produce finer nano-level fibers, significantly enhancing the filtration efficiency and strength of the nonwoven fabric.
- High Production Capacity Design: The new meltblown equipment can further increase capacity while ensuring product quality, meeting the demand for large-scale production.
5. Application of Digital Twin Technology
Digital twin technology is gradually being applied to the development and production of nonwoven fabric equipment. Through real-time linkage between virtual models and actual equipment, companies can simulate various situations in the production process, identify and solve potential problems in advance, and improve equipment stability and production efficiency.
- Virtual Debugging and Optimization: Before equipment installation and debugging, digital twin technology can be used for virtual testing to optimize production parameters, reducing actual debugging time and costs.
- Remote Monitoring and Maintenance: During equipment operation, the digital twin system can monitor the status of each component in real-time and issue warnings before failures occur, helping companies perform preventive maintenance and reduce equipment failure rates.
More Blog
Turkey Rubber & Plastics Exhibition Plastic
Turkish Rubber and Plastics Exhibition is a major annual event with UFI cert.
2024-08-06
Hubei Huiyu Machinery Equipment Co., Ltd. produces various PP production lines.
2024-08-06
Shenzhen Rubber & Plastics Exhibition
The 18th Shenzhen Plastics and Rubber Exhibition in 2024 is coming.
2024-08-06
HY-3.2m S Nonwoven Fabric Machine is loading to India Mundra port
the HY-3.2m S Nonwoven Fabric Machine loading to India Mundra port represents a new chapter in the evolution of the nonwoven fabric industry. We are proud to be leading the way with our advanced technology and commitment to excellence
2024-09-30