Technical parameter
product | breadth m |
exportation Ton/Day |
speed (m/min) |
Installed capacity (KW) |
Power consumption kw/Ton |
Machine size |
(m) | ||||||
S Production line | 1.6m | 4-5 | 150 | 280 | 800kw/h | 10*20*10.5m |
2.4m | 6-7 | 320 | 14*20*10.5m | |||
3.2m | 9 | 400 | 17*20*10.5m | |||
SS Production line | 1.6m | 8-9 | 300 | 400 | 800kw/h | 10*30*10.5m |
2.4m | 12-13 | 550 | 14*30*10.5m | |||
3.2m | 16-17 | 650 | 17*30*10.5m | |||
SSS Production line | 1.6m | 13-14 | 350 | 630 | 800kw/h | 13*30*10.5m |
2.4m | 20-21 | 800 | 15*30*10.5m | |||
3.2m | 27-28 | 1100 | 17*30 10.5m | |||
SMS Production line | 1.6m | 10-11 | 300 | 760 | 1200kw/h | 15*30*10.5m |
2.4m | 15-16 | 950 | 18*30*10.5m | |||
3.2m | 20-21 | 1250 | 21*30*10.5m | |||
SMMS Production line | 1.6m | 13-14 | 400 | 1100 | 1400kw/h | 18*40*10.5m |
2.4m | 21-22 | 1350 | 20*40*10.5m | |||
3.2m | 28-30 | 1700 | 22*40*10.5m | |||
SSMS Production line | 1.6m | 15-16 | 450 | 900 | 1300kw/h | 18*30*10.5m |
2.4m | 23-24 | 1250 | 20*30*10.5m | |||
3.2m | 30-32 | 1600 | 22*30*10.5m | |||
SSMMS Production line | 1.6m | 18--19 | 500 | 1500 | 1400kw/h | 46*18*10.5m |
2.4m | 26--27 | 1700 | 46*20*10.5m | |||
3.2m | 33--35 | 1900 | 46*22*10.5m |
Product display
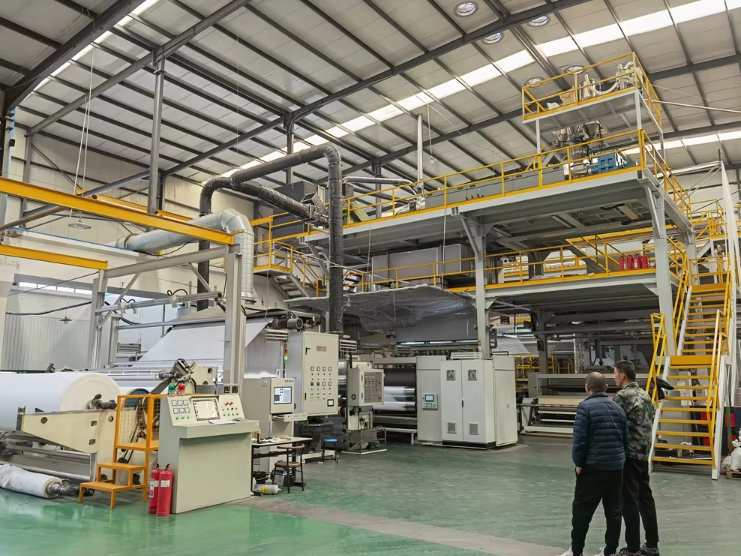
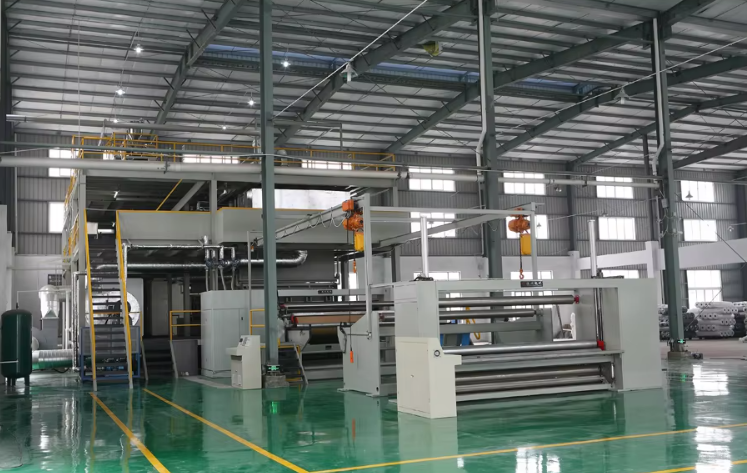
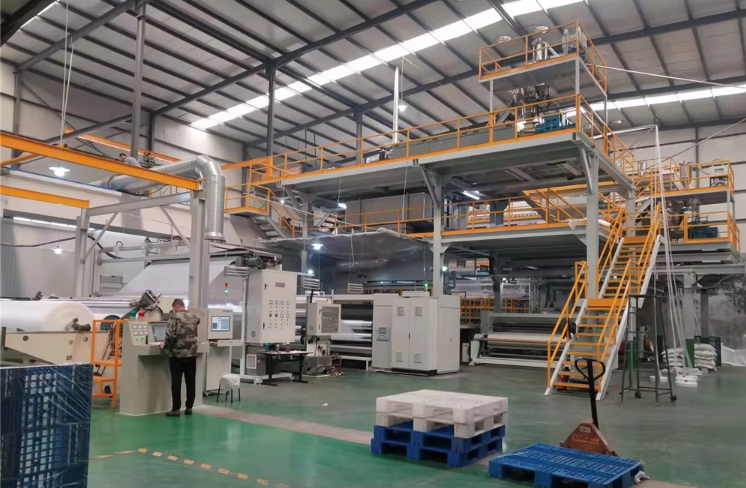
Below is a partial sample diagram of the customer installation completed
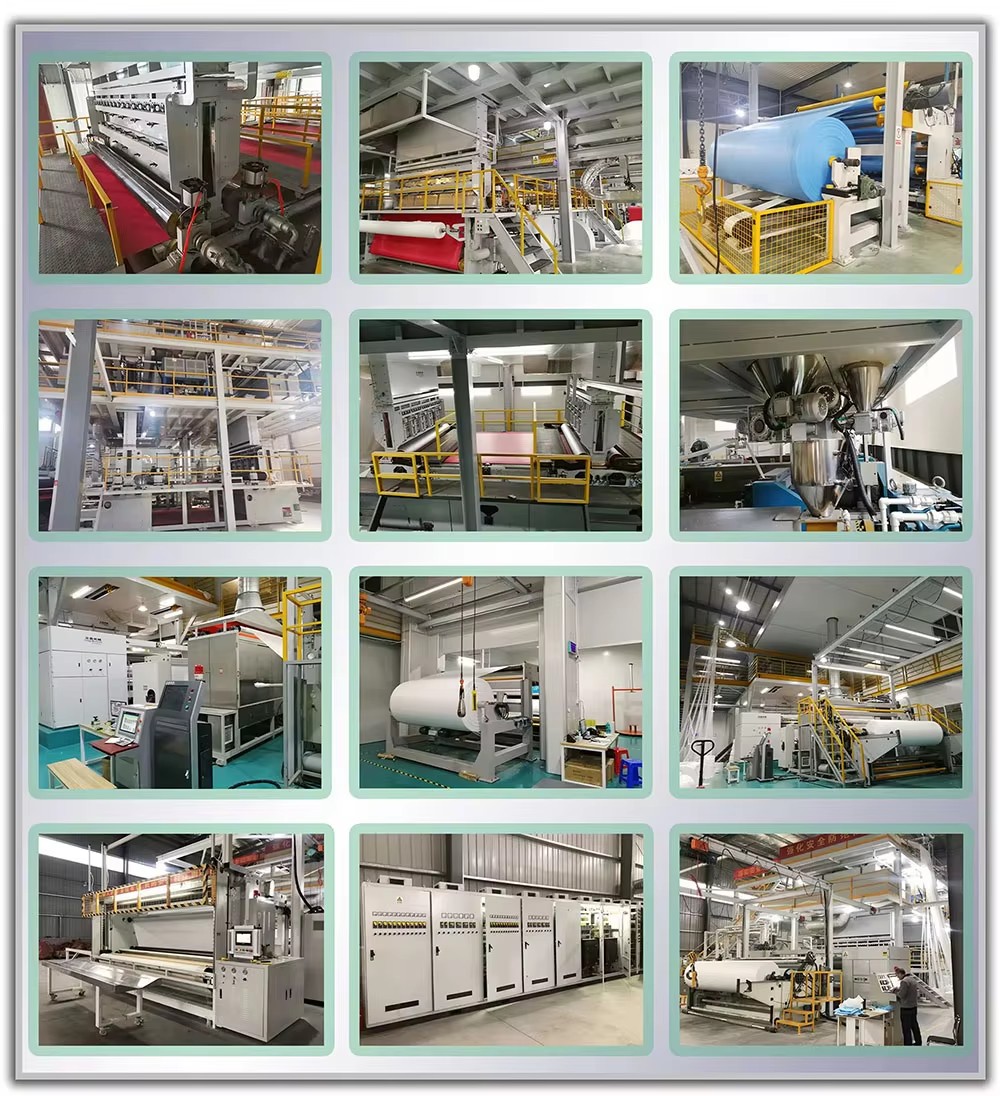
The above finished products are installed and debugged by our company, and smoothly put into operation. They're all real shooting parts.
Partial display
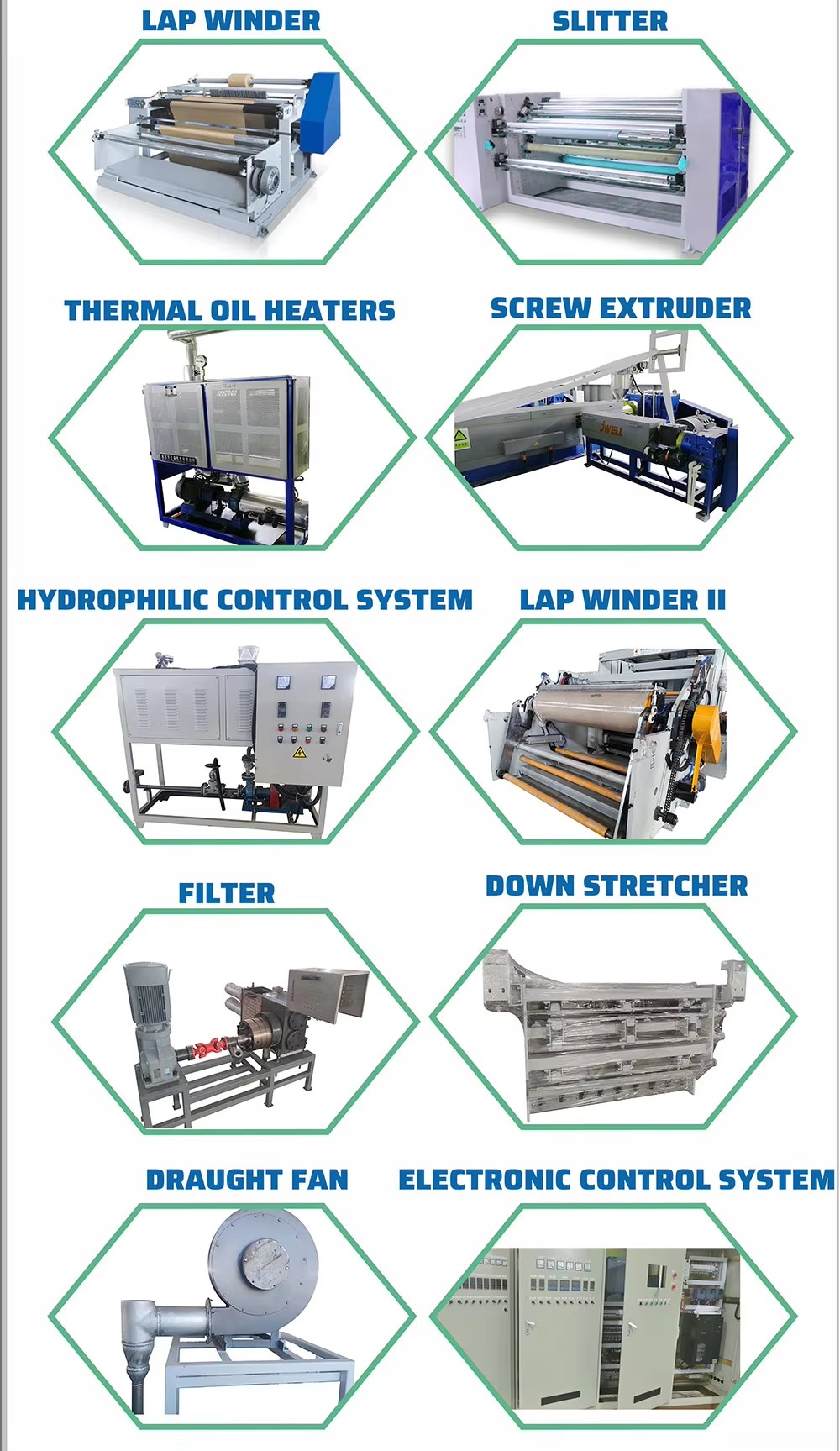
Tips:
All parts of our company are covered by replacement warranty service. If abnormal damage occurs during the work, our company will carry out after-sales service to the end.
About us
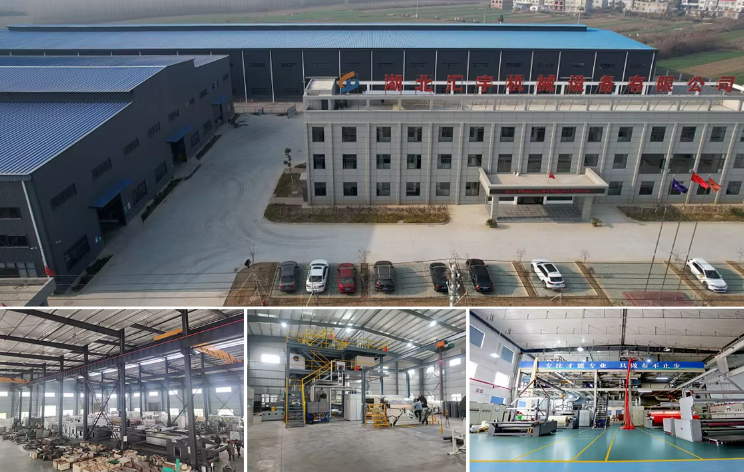
Hubei Huiyu Machinery Equipment Co. Ltd
Hubei Huiyu Machinery Equipment Co. Ltd was established in 2017, with an area of 33,000 square meters and more than 50 employees. Located in the beautiful Jianghan Plain,Located near the city of nonwoven fabrics, the company keeps abreast of the latest technological developments in this field. With more than ten technical backbone members and a professional design team with more than 15 years of experience in research, development and production of nonwoven fabric equipment, the company is specialized in manufacturing S/SS/SSS/SMS/SSMS/SSMMS spunbond and meltblown nonwoven fabric production lines and has gained a good reputation in the industry.
Our company has its own research and development facility and laboratory, and strives for excellence in production, research and testing. With "precision in production, quality for victory" as our service tenet, we are committed to building an internationally renowned brand.
Since 2019, Huiyu has obtained ISO9001, CE and SGS certifications, and our production lines have been exported to many countries such as India, Brazil, Turkey, Saudi Arabia and Iraq. With a professional foreign trade sales team, enthusiastic customer service, detailed technical explanations and onsite guidance, we have won unanimous praise from customers at home and abroad, and achieved international business development. We at Huiyu welcome all to negotiate and cooperate with us.
Tips
All our machines have CE ISO certification, quality assurance. Our company perfect after sale, once purchased, lifelong maintenance.
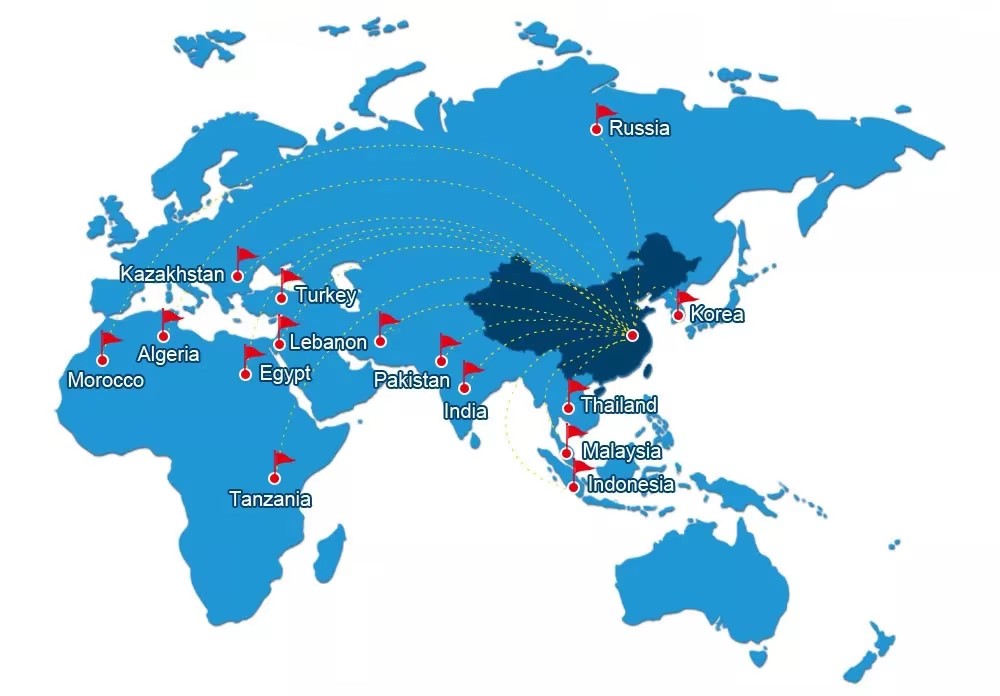
Advantages:
1. Full quality control, providing personalized and cost-effective nonwovens to help customers save costs.
2. Focus on non-woven equipment research and development for 14 years, and install and operate more than 400 lines around the world.
3. Japan imported high-precision CNC machine tools, the processing of key parts are completed in the company, to ensure that every customer to provide high-quality machine tools.
4.A machine after-sales service team of more than 20 people to ensure that customers can quickly, professional and timely installation and commissioning.
< class="image image_resized" style="width:1000px;">
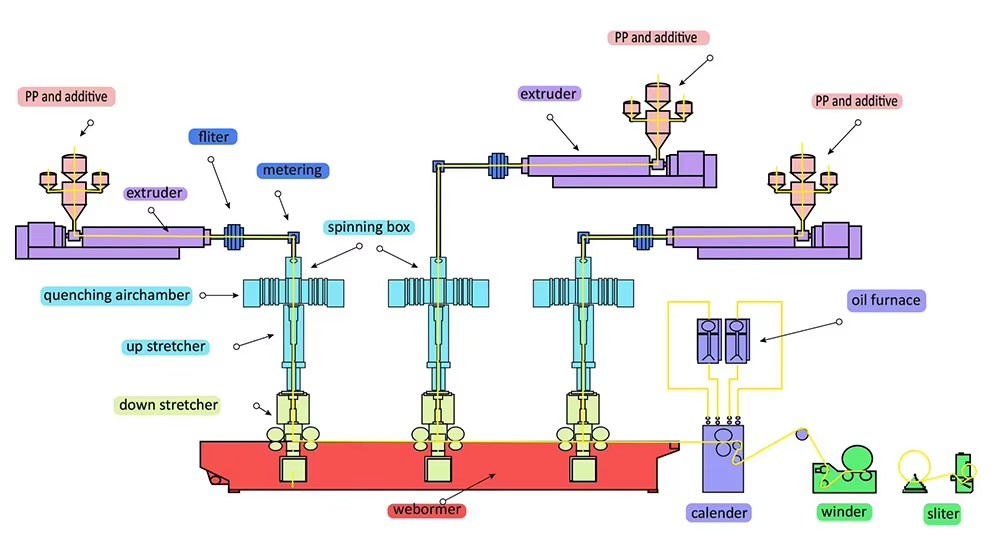
Flow chart
This is the process flow chart of spunbond non-woven production line. The whole assembly line has clear structure and perfect function. The role and function of each link are clearly visible.
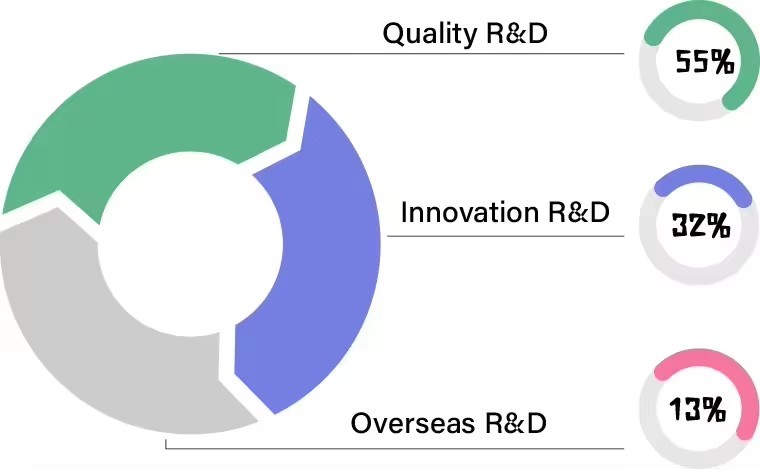
Research and development
In product development, Huiyu company at all costs to explore more advanced non-woven technology.
The introduction of domestic and foreign excellent scientific research results, transformation and improvement. Hire great engineers and invest more than 32% in innovation each year.
Exhibition and customer photos
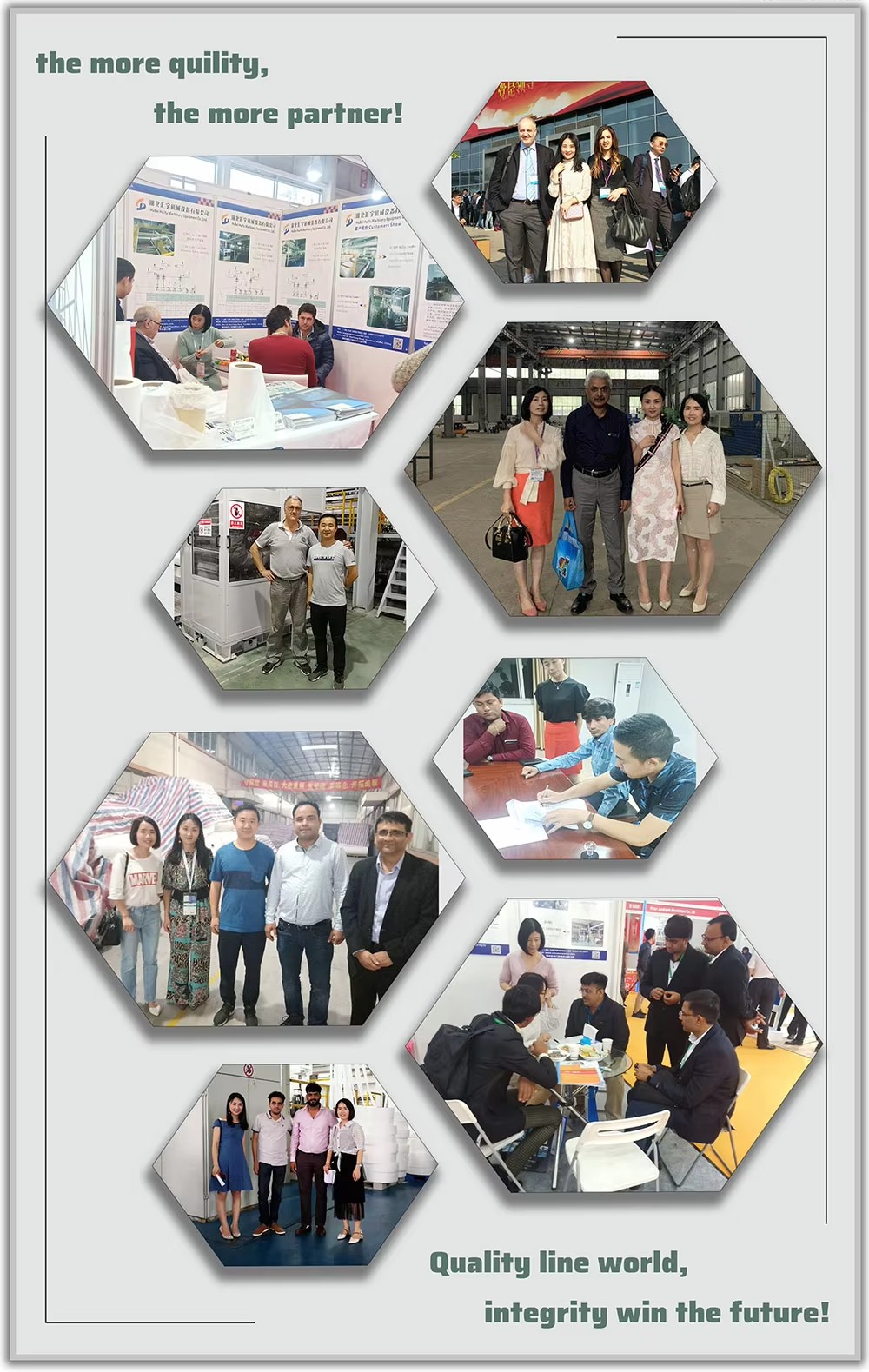
Product packaging
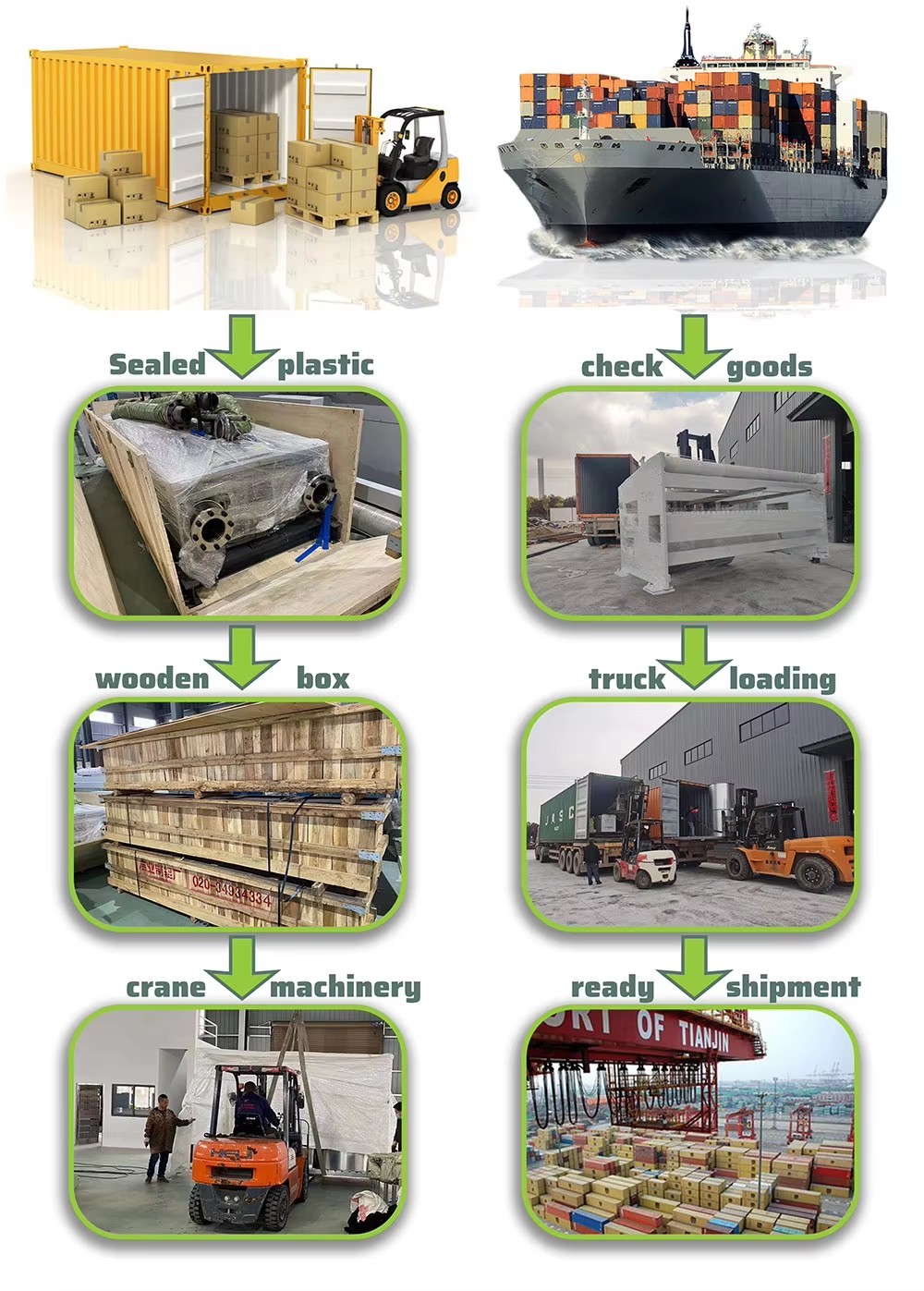
FQA
Q1. Do you offer installation services?
Yes. We will send technicians to overseas sites to guide and help install the machines, while training the customers' workers until they can produce the fabrics themselves.
Q2, What is your warranty period?
We offer a 1-2 year warranty on different parts.
Q3. What is your delivery time?
Under normal circumstances, the production time takes 3-6 months. When you place your order, we will confirm your exact time.
Q4. Are you a factory or a trading company?
We are a factory with export rights. We manufacture our own machines and export them to our customers.
Q5. Where is your factory located? How can I visit it?
Our factory is located in Tianmen City, Hubei Province, which is famous for the manufacture of non-woven machinery. You can fly to Wuhan Tianhe Airport, or take the high-speed train to Tianmen South Station, I will pick you up.